Cam Design Equations
S a 1 qw a 0 Let H Total follower rise Stroke b angular rotation of the cam corresponding to the total rise of the follower. Writing these three equations in matrix form gives.
Cam Design Equations Replace Graphics Machine Design
Use positive numbers if opening is BTDC and closing is ABDC for the intake and opening is BBDC and closing.
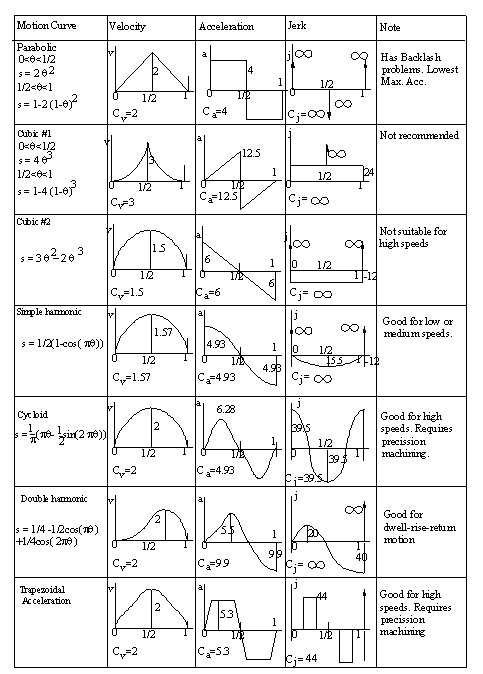
. This paper presents a method for designing of a radial cam on the worksheet of Mathcad including the calculation of followers displacements values of its ve-locities and accelerations the optimization of the contour of a cam by choosing the. Kwakernaak and Smit 1968 formulated the problem of finding Cam. Curve development and selection is one of the primary steps in the design of any cam-follower system.
Equation at the desired design speed given the Cam-follower system dynamic characteristics. 0 0 6 12 20 3 4 5 1 1 1 2 1 0 2 h a a a b b b b b b Solving for ao a1 and a2 gives. A typical design evolutionary process will proceed as a series of trade.
In Figure 6-13 only part of the cam profile AK is displayed. Design of the Cam Profile. Eccentricity e Disc Cams for Translating Follower Eccentricity angle α Linear and Cylindrical Cams for Translating Follower Pivot Distance y Disc and Linear Cams for Swinging Arm Arm Length l a Disc and Linear Cams for Swinging Arm Reaction Arm l r Disc and Linear Cams for Swinging Arm Speed ω Disc and Cylindrical Cams.
V OK A is not continuous infinite jerk spikes Is not a good design yet Despite this deficiency this profile is popular for cam design in low-speed applications because it is easy to manufacture 81 Simple HarmonicMotion 27. Cam synthesis design results For Cam synthesis design results are used cam phase angles. Where R b is the base circle radius L is lift and a is acceleration.
θ 4 150 deg. S h βθ h2Π sin 2Π βθEqn3. Equations 1121314151 and 61 represents 21 equations with 21 unknowns 20 coefficients C 019 and maximal value of acceleration A.
β Cam rotation angle at which the follower reaches the maximum height lift. A symmetric cam with timing 25-65-65-25 has intake and exhaust centers of 65180-252 110 ATDC and 110 BTDC respectively. XT Linear distance corresponding to period θT in.
3 4 5 10 15 6 b q b q b q s h h h. Later chapters include investigation of the pressure angle cam curva-ture cam torques lubrication materials and necessary fabrication tolerances among other things. Base circle diameter 100 mm.
The base circle and lift are positive and their sum normally approximates the radius of the cam bearings. Since the rise occurs in. We have the following data as input.
Where s Displacement of follower at a cam rotation angle θ. This method was apparently tried by many of the car companies but was not adopted by any one because this method uses an incomplete polynomial to specify the profile. Figure 6-13 Profile design of translating cam follower.
θ 1 40 deg. R c R b L a 180 π2. Graphical Cam Profile Synthesis 71 Knife Edge Follower 72 Traslating Roller 73 Traslating Offset Roller 74 Overturning Moment in Traslating Flat-Faced Followers 75 Oscillating Flat-Faced Follower 8.
Once the design is complete it is then the grinders responsibility to translate this profile to the cam as true as. Also assume when s 0 q 0 rise is to start when t0. Manufacturing considerations Literature 2.
Calculating CAM Velocity for Cycloidal Motion. Assume the cam turns clockwise. Lobe Separation Angle or Lobe Displacement Angle The angle between the centerlines of intake and exhaust lobes expressed in camshaft degrees.
5 the minimum allowable cam radius is simply equal to the maximum or minimum value of y0 hence r follower maxjy0j 6 The largest contact point o set will occur at the peak follower velocity. Equations and a few boundary condition equations each having different effects in all of the domains. R Radius of.
θ 3 110 deg. θT Period deg of cam movement. Area of a circle radius x radius x 314159.
Circumference of a circle diameter x 314159. DESIGN OF A RADIAL CAM FOR THE CAM-FOLLOWER MECH-ANISM. S a 1 t a 0 Assuming constant angular velocity for the input cam w since t qw.
The displacement of a simple harmonic motion follower is governed by the following equation. At the beginning of motion the knife edge of the follower contacts the point of intersection A. θ 2 70 deg.
Total lift 80 mm. For example a COMP Cams XE274H-10 hydraulic cam lists the following opening and closing points for a checking lift of 0006 inch. L Total lift in.
Radius of curvature 9. θ 5 180 deg. Equation describing a linear motion with respect to time is.
Degrees of duration opening closing 180. Since from the cam geometric analysis we know that s y0. For a flat tappet cam the radius of curvature is related to other cam parameters as follows.
The designer uses these equations to simultaneously solve for constraints in all of the domains. For the ease of the discussion lets take the example of creating the cam profile of a knife edge follower. In this figure let.
IO 31-degrees BTDC IC 63-degrees ABDC EO 77-degrees BBDC EC 29-degrees ATDC. A0 10h a1 -15h a3 6h The final polynomial equation for follower displacement is. Aan A Heinloo M Allas J.
Suranaree University of Technology. Hence Intake Duration 31 180 63 274 degrees at 0006-inch lift Exhaust Duration 77 180 29 286 degrees at 0006-inch lift. Actual valve lift cam lift x rocker arm ratio - valve lash.
θ 6 220 deg.
Imp Lensmaker S Equation Non Negligible Lens Thickness Lens Surface Mcat
Four Fourth Roots Of Unity Complex Numbers Part 1 Complex Numbers Unity Education
Image Result For First Principle Of Thermodynamics Delta U Q W Derive Every Erm Deeply Momentum Physics Physics Lessons Thermodynamics
Manufacturing Engineering Vs Mechanical Engineering Numerical Method For Engineers Open Met Numerical Methods Manufacturing Engineering Engineering Subjects
Gm Jackson Physics And Mathematics How To Derive Christoffel Symbols And The Covariant Derivative Physics And Mathematics Mathematics Math
Belum ada Komentar untuk "Cam Design Equations"
Posting Komentar